Robert and John Westerlund started the company that would become Construction Forms, Inc. from a rented garage in Los Angeles, CA in the 1950s. Their innovations and work ethic were instrumental in the birth of concrete pumping across North America. A few large projects allowed them to expand their manufacturing to Miami, FL and Cedarburg, WI by 1969.
The Con Forms team was successful in designing and producing many accessories to improve the concrete pumping process, but extending the life of steel pipes used in abrasive environments became a high priority. Induction heating of steel had been known since Michael Faraday identified the capabilities in 1831. Following World War II, a variety of manufacturers continued to refine and improve the process to produce localized case hardening for automotive parts.
The Westerlunds recognized this through-hardening process would be ideal to improve the longevity of pipes used in concrete pumping. In 1989, they purchased and installed their first Induction Heat Treat Machine at their new facility in Grafton, WI. As experienced engineers, they knew that many other industries could make use of abrasive-resistant steel pipe and Ultra Tech was born.
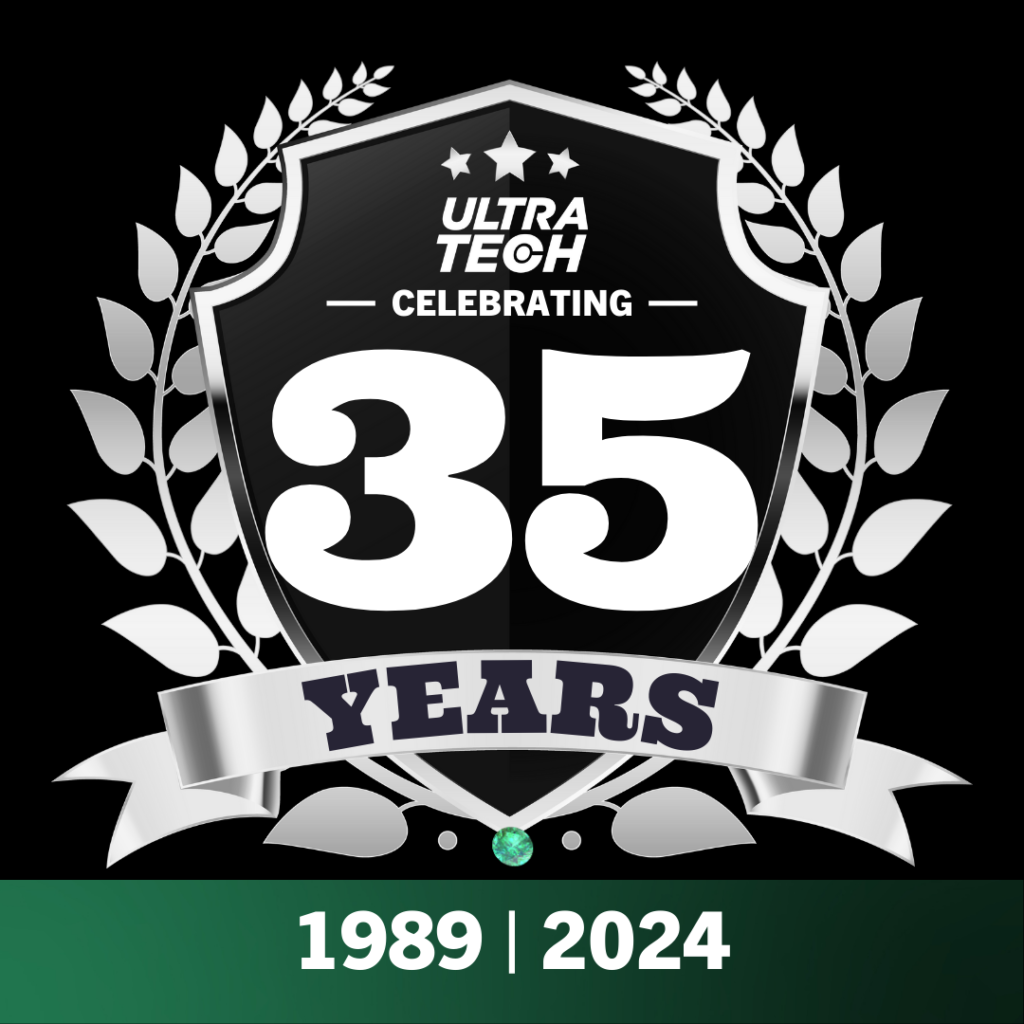
They would add an induction bender and second heat treater in 1995 at a new facility in Port Washington, WI, and production of our flagship Ultra 600 abrasion-resistant steel began to grow dramatically.
One early, large-scale international project was at the Peruvian Yauliyacu Copper mine in 2000. They installed over 5km of UT 600 in their tailings line and continue to use Ultra 600 today.
Mining quickly became a key application for the more durable, cost-effective Ultra Tech steel. A variety of operations recognized the savings in materials and maintenance that UT 600 provides.
CF Industries (currently Mosaic Company) was one of the first to install UT600 for phosphate mining in Florida (2006). Additional international phosphate operators Nutrien (Aurora, NC) Maaden (Saudi Arabia) and OCP Group (Morocco) have joined the ranks of UT 600 users.
Current Ultra Tech customers include Nevada Gold Mines, Morenci Copper mine, Voiseys’s Bay Nickel mine, Vale Canada, Divak Diamond Mine in the Northwest Territories, and Pretium Bruce Jack (now New Castle) Gold and Silver mine.
Over 825 miles of Ultra Tech pipes have been installed globally.
Today, Ultra Tech is more than just straight pipe. Bends, fittings, hoses, diversion valves and couplings are all part of the Ultra Tech portfolio. And they continue to innovate with the introduction of the cast iron XLE elbow for pneumatic applications (2023) and the newest forged, Hevi-Duty™ Coupling for mining introduced in 2024.
As awareness about the environmental impact of mining operations has grown, Ultra Tech has become an exceptional choice to lower an operation’s carbon footprint. The use of induction-hardened, abrasion-resistant UT 600 can keep 3-6 times as much new raw pipe from being produced.
Ultra Tech is proud to celebrate 35 years of success and innovation.