Eck Industries, Manitowoc, Wis., operates a specialty aluminum foundry that manufactures various sand-cast aluminum parts for automotive, defense, and other industries. The foundry operates 24 hours a day, seven days a week, and makes more than 3,500 different cast aluminum parts weighing as little as 1⁄2 pound to more than 2,000 pounds. The company decided to expand the foundry and install a thermal sand reclamation system to reclaim up to 6,000 lb/hr of sand for reuse in the casting operation. Because of the sand’s abrasiveness, the company needed special pipe and elbows in the system’s conveying lines.
The company uses the airset sand casting method when making cast aluminum parts. In doing so, the company uses a sand mixture consisting of silica sand, a two-part resin, and a catalyst to make an aluminum part casting mold. After a casting mold is prepared, molten aluminum is poured into it and left to cool and harden. The mold is then taken apart and the sand is chipped away to reveal a solid aluminum part that’s ready for final cleanup work to smooth any rough areas.
Conveying silica sand causes problems:
Since the foundry makes so many cast aluminum parts, it goes through a lot of non-reclaimed silica sand when making various molds. To ensure that enough sand is on hand to maintain high production rates, semi-trucks deliver 66 tons of sand to the foundry every day. Each semi-truck has a PD blower that conveys the sand from the truck into large storage silos located above the foundry. From the silos, the sand is pneumatically conveyed into the foundry to two mixing stations, and from the mixing stations the sand mixtures are conveyed to various points of operation for use in the casting molds.
The foundry’s two dilute-phase conveying systems originally used 4-inch diameter, Schedule 80 black iron pipe to move the sand from the trucks to the silos and from the silos throughout the foundry. However, the abrasive sand would wear through the pipe in about 6 months and spill out onto the foundry’s roof or floor, depending on where the pipe was located.
“When a pipe failed, we had to shut down the conveying and production lines and sweep up the sand and repair or replace the pipe,” says Tom Gass, vice president of material purchasing at Eck Industries. “We had to throw away the spilled sand, which sometimes amounted to a couple of tons.”
The foundry had to keep the conveying and production lines shut down until the repairs were finished. “When a pipe blew out, we’d first patch the hole to get the lines back up as fast as possible because when we’re not transferring sand, we’re not making castings,” says Dennis Fischer, Eck Industries maintenance manager. “However, after about three months, the patch would wear out, and then we’d have to replace the five to forty-foot-long pipe section, which meant we had to shut down the lines and reduce the production rate again.
“Depending on where the pipe was located, we sometimes had to rent a crane to repair or replace the pipe section, which is very expensive and time-consuming. Using the crane also caused safety concerns because the operator would be suspended high off the ground in the crane bucket working with a heavy pipe section, sometimes in the middle of winter in below-zero wind-chill conditions.”
Increasing pipe operating life:
Eck Industries needed to find a way to increase the pipe operating life to decrease production downtime and maintenance costs. The company contacted a nearby pipe system supplier to inquire about the supplier’s line of abrasion-resistant pipe. Ultra Tech Pipe, a division of Construction Forms Inc., Port Washington, WI, supplies the special pipe to companies that pneumatically convey high volumes of abrasive bulk solids.
Shortly after talking with Ultra Tech Pipe, the company began replacing black iron pipe sections with the supplier’s 4-inch diameter, Schedule 80, abrasion-resistant pipe whenever the old pipe wore out. “Since this pipe can last up to six times longer than black iron pipe, we significantly reduced downtime and maintenance costs over the years because once a pipe section was replaced, it didn’t have to be touched again for two to three years,” says Gass. “We started replacing the pipe more than ten years ago, and by now, more than ninety percent of our conveying systems’ lines consist of the abrasion-resistant pipe. We have just a little more black iron pipe in our inventory that needs to be used before everything will be completely switched over.”
Expanding the foundry:
In 2006, the company wanted to increase the foundry’s production capacity without having to significantly increase the amount of sand it purchased. To do so, the company planned to expand the foundry and install a thermal sand reclamation system to reclaim up to 6,000 lb/h of sand that would be reused to make casting molds. According to Gass, since the company had a good working relationship with the pipe supplier and was happy with its abrasion-resistant pipe, it was an easy decision to specify the supplier’s pipe and other components when designing the reclamation system.
“Before installing the equipment in the foundry expansion, we had two supplier reps from Ultra Tech come to the foundry to help us and our general contractor, Schaus Mechanical, engineer the reclamation system’s conveying lines,” says Gass. “We had many discussions and produced numerous drawings and schematics for the pipe runs. We wanted to know exactly where to install the pipe and where to position the equipment to make the reclamation system the most effective and efficient.”
Once the reclamation system’s conveying line plans were finalized, Ultra Tech delivered approximately 360 feet of 4-inch diameter abrasion-resistant pipe, 16 elbows, and one lateral that joins two conveying lines into one.
The abrasion-resistant pipe:
The Ultra 600 abrasion-resistant pipe is made via a proprietary chemistry and process that produces a long-lasting pipe without requiring an internal liner or coating. The pipe’s 600 Brinell hardness inner wall penetrates 25 percent of the pipe thickness before slowly transitioning to the outer wall, which is rated at 250 Brinell. (An equivalent standard carbon steel pipe is only rated at 120 to 125 Brinell both inside and out.) The pipe’s 600 Brinell interior provides outstanding abrasion resistance, while its 250 Brinell exterior provides sufficient ductility to absorb shock and vibration, and prevent the pipe from cracking or breaking. The pipe has no internal abrasion-resistant liner or coating, so there’s little risk of cross-contamination because there’s nothing that can abrade off or come loose during conveyance.
The pipe, which is available in up to 50-foot lengths, has the same weight per foot as standard carbon steel pipe, so it doesn’t need additional support if the pipe is going to be suspended from a ceiling. The pipe is manufactured in standard National Pipe Size (NPS) diameters ranging from 2.5 to 24 inches in both Schedule 40 and Schedule 80 thicknesses (as well as larger custom sizes) and doesn’t require special fittings when attaching it to any other matching NPS-diameter pipe. The pipe’s wall thickness depends on the pipe’s diameter. For example, a 2.5-inch diameter, Schedule80 pipe has a 0.276-inch nominal wall thickness, while a 24-inch diameter, Schedule 80 pipe has as much as a 0.5-inch nominal wall thickness. The 4-inch diameter, Schedule 80 pipe installed in Eck Industries’ foundry has a 0.337-inch wall thickness.
The pipe can be used in both dense- and dilute-phase pneumatic conveying systems to convey silica sand, grain and rice, glass materials, ceramic beads, pulverized coal, fly ash and bottom ash, and any other abrasive materials used in powder and bulk solids industries. And since it only contracts and expands a negligible amount when exposed to extreme cold and heat, the pipe can be installed both inside and outside a facility.
Ultra Tech can manufacture the pipe in standard sections that can be cut to length in the field or custom sections with flanges already welded on. Ultra Tech also manufactures abrasion-resistant, standard 45- and 90-degree elbows, as well as custom elbows and any other types of fittings necessary to complete a pipe system, all of which are made using the same proprietary material as the pipe.
Long-lasting pipe continues to deliver positive results:
After completing the expansion project, Eck Industries started up the thermal sand reclamation system. “After a cast aluminum part is made, we break down the mold until the sand is grain size and then reclaim it,” says Gass. “The sand is dense-phase, conveyed through the abrasion-resistant pipe in slugs, and transferred into a silo above the reclaimer, which is basically a big oven that burns off all the impurities. From the reclaimer, the sand is conveyed into a silo and then to another mixing station located in the foundry, where it’s mixed with a two-part resin and a catalyst before being poured into a casting mold. The conveying system moves about one thousand pounds of sand three hundred feet in two hundred seconds, and when we’re operating at full capacity, we can reclaim close to six thousand pounds of sand per hour.”
“Even though the supplier’s pipe costs a little more than the black iron pipe, we’ve seen a cost savings over the long run because of its extended operating life,” says Gass. “We’ve also seen a significant decrease in our operating costs because of the reduction in downtime, maintenance, and crane rental costs. To further reduce our maintenance costs, we don’t worry about repairing the pipe with patches anymore. After we install the pipe, it will stay in place until it wears out and then we’ll replace it.”
To help the company predict potential pipe failures, Ultra Tech regularly travels to the foundry to perform pipe wall thickness tests. Fischer says, “This gives us an idea of when we’ll need to replace the pipe and allows us time to line up a crane in advance and schedule things to minimize downtime.”
According to Gass, the company plans to continue using the supplier’s pipe in the future. “We have a project in the works right now, and we’re going to use fifty to one hundred yards of their three-inch diameter pipe. We’re still doing some pre-engineering work before we move forward with it, and we anticipate doing another major expansion sometime in the next year.”
Originally published March 2009 – Power and Bulk
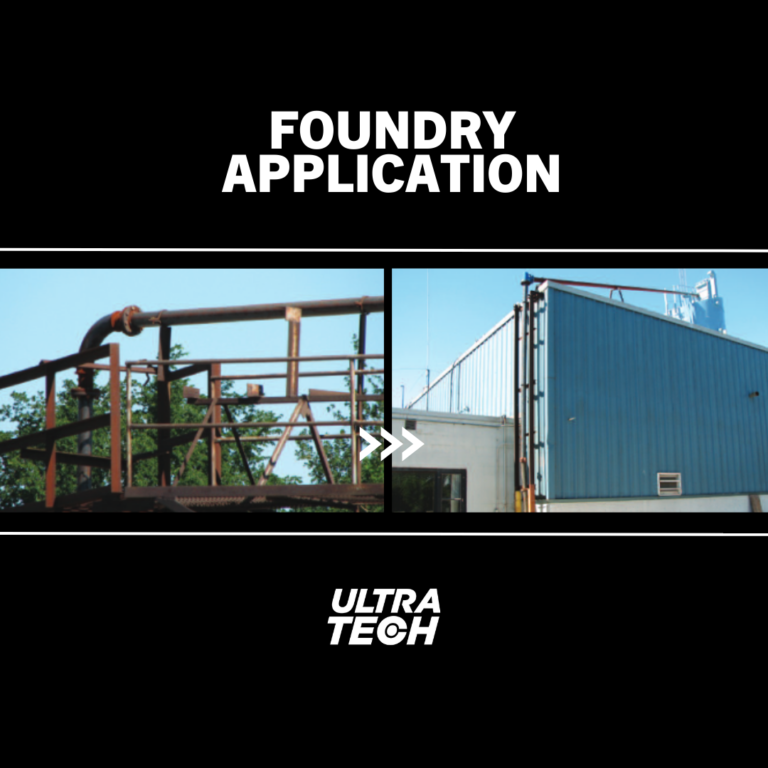